„Als Industrie haben wir der Politik bisher zu wenige Angebote gemacht“
Anders als die meisten Mitbewerber, arbeitet die Maag GmbH fast ausschließlich mit Polypropylen – kurz PP. Das ist ein thermoplastischer Kunststoff, nah verwandt mit Polyethylen, aber etwas härter und thermisch höher belastbar. Welche Chancen sich dadurch bieten und wie es das Unternehmen im nördlichen Sauerland zudem geschafft hat, strategischer zu denken, hat uns Ansgar Schonlau, Geschäftsführender Gesellschafter bei Maag, im Interview erzählt.
Herr Schonlau, die Kreislaufwirtschaft ist der Weg der Zukunft. Was verstehen Sie bei darunter?
Wir nähern uns dem Thema Nachhaltigkeit über die 17 Ziele für eine nachhaltige Zukunft der Vereinten Nationen. Kreislaufwirtschaft bzw. Recycling ist ein Beitrag dazu. Speziell das Thema Recycling sehen wir als elementare Voraussetzung für eine dauerhaft klimaneutrale Industrie. Dieser Prämisse müssen sich alle Maßnahmen im Bereich Klimaschutz und Klimaneutralität unterordnen.
Die EU hat im Rahmen ihrer „Plastics Strategy“ eine Pyramide erstellt, bei der Müllvermeidung oberstes Thema ist. Ich glaube, hier ist die erste Fehlinterpretation möglich. Viele Leute denken, sie sollen Plastik um jeden Preis vermeiden und eine dicke Folie dünner machen. Wird jedoch ein dicker Mischverbund dünner, ist er weiterhin nicht recyclingfähig. Meiner Meinung nach geht es bei der Pyramide darum, Ressourcen einzusparen, wo immer es geht. Und wenn sie genutzt werden, dann müssen sie auf jeden Fall recyclingfähig sein, das gilt auch für Verpackungen.
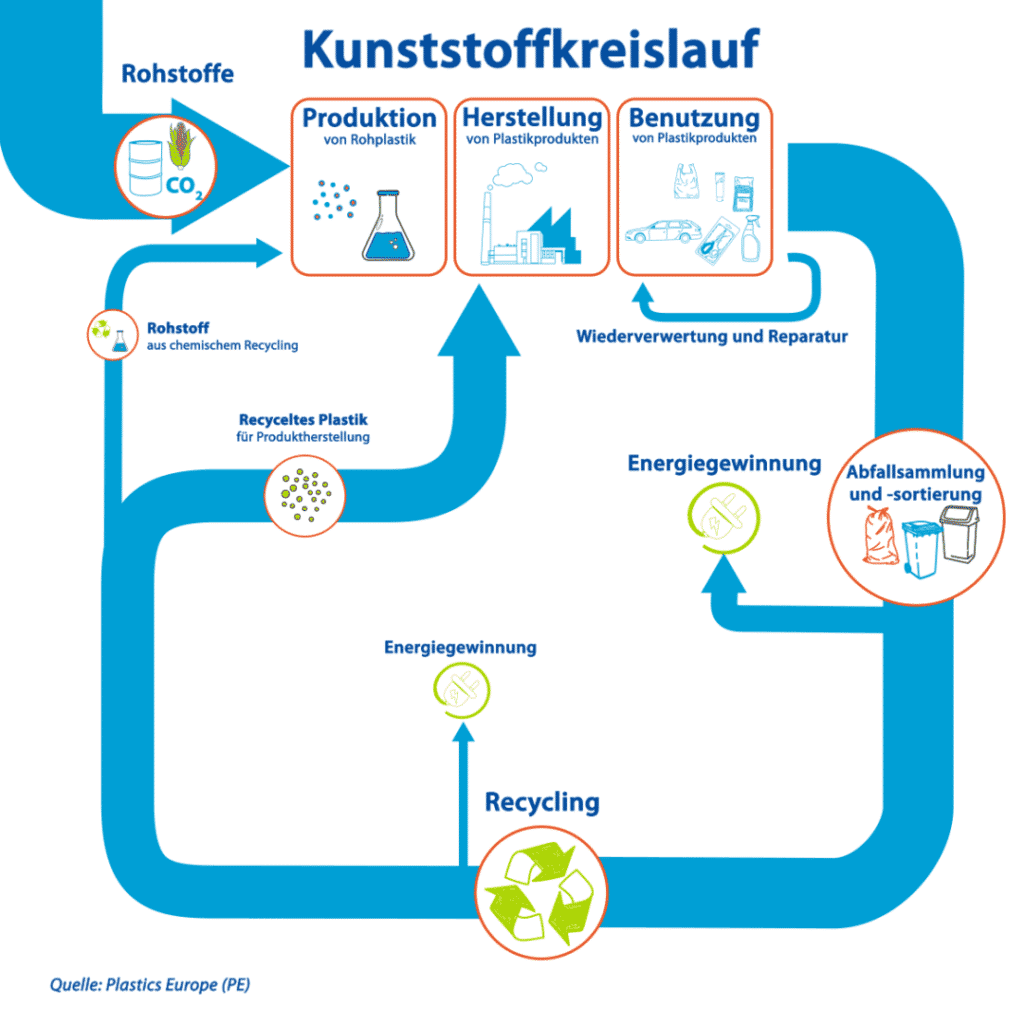
Wie gehen Sie diesen Weg bei Maag?
Bei Maag glauben wir, dass Recyclingfähigkeit auf Dauer nicht die Messlatte sein wird. Wir leben von Kreislauffähigkeit. Das bedeutet, dass grundsätzlich jeder Kunststoff recyclingfähig ist, wenn er als Monomaterial ankommt. Das hilft allerdings nicht, wenn es keinen Abnehmer für das Material gibt.
Deswegen haben wir eine durchgängige Lösung gesucht. Die Frage ist: Was passiert mit diesem Rezyklat? Denn momentan gibt es einen Überhang an Polyethylen (PE) und Polyolefin, weil es für die recycelte Ware nicht genügend Abnehmer gibt.
Wir folgen nicht der Theorie, dass das daran liegt, dass Rezyklate zu teuer sind. Wir gehen aber davon aus, dass PP-Rezyklaten einfach mehr Wege offenstehen. Nach Gesprächen mit Extrudeuren und Herstellern von Extrusionsanlagen ist der Einsatz von Rezyklaten in flexiblen Lebensmittelverpackungen und in daran angrenzenden Bereichen im Moment noch sehr unrealistisch. Die Qualität ist einfach nicht ausreichend. Gleichzeitig ist es schwierig, das Rezyklat in einer chemisch-technischen Verpackung, beispielsweise einer Nachfüllverpackung für Waschmittel, einzusetzen. Denn auf einem Extruder werden sowohl Lebensmittelverpackungen als auch die chemisch-technischen Produkte gefahren. Bei einem Wechsel sind aufwändige Spülprozesse notwendig, damit keine Kontamination erfolgt. Dabei entsteht so viel Abfall, dass es keinen Sinn macht.
Und das ist bei Polypropylen anders?
Ja, PP eignet sich hervorragend für die unterschiedlichsten Verpackungsarten und die unterschiedlichsten Märkte, wie beispielsweise Kaffee, Butter, Nüsse, Tierfutter, Feuchttücher oder chemisch-technische Produkte.
Unsere kreislauffähigen Verpackungen sind nun auch bei den dm-Bio-Marken-Produkten Tassenkuchen, Pancakes und Kaiserschmarrn zu finden.
Im sogenannten „zweiten Leben“ gibt es viel breitere Anwendungsgebiete. Man kann das Rezyklat im Spritzguss, in der Automobil- oder in der Bauindustrie einsetzen und fossile Rohstoffe 1:1 ersetzen.
Und schon sind wir dem Thema Klimaneutralität ein Stück näher. Dazu muss PP aber im gelben Sack landen und separat sortiert werden. Das passierte bisher allerdings noch nicht. PP wurde bislang noch nicht als flexibles Material aus dem Stoffstrom geschleust. Es gibt mittlerweile jedoch einige Unternehmen, die sehr intensiv daran arbeiten. Erste Beispiele liefern PreZero und Swedish Plastic Recycling (Svensk Plaståtervinning). Ab 2023 werden alle Kunststoffverpackungen aus schwedischen Haushalten recycelt und “Polypropylenfolien” als separater Sortierweg eingeführt. Damit sichert Schweden die Recycling-Infrastruktur für flexible PP-Verpackungen und schließt den Kreislauf. Deshalb bin ich mir sicher, dass der PP-Flexstrom in Gang kommt..
Die Recyclingquote ist aktuell nur gering. Was können wir tun, um die geforderte Quote zu erhöhen?
Wir müssen den richtigen Ausgangswerkstoff nutzen. PP hat hervorragende Eigenschaften in der Breite der Verpackungen und in der Breite der Märkte. Es eignet sich aufgrund seiner Schmelzflusseigenschaften zudem sehr gut für das Recycling. Und es existieren Anschlussmärkte. Sobald der PP-Flexstrom in Gang kommt, werden auch die Recyclingquoten steigen. Bislang sind jedoch noch 90 Prozent der Hersteller auf PE ausgerichtet.
Da fällt es uns leichter, diesen neuen Weg zu gehen. Denn wir müssen unsere Maschinen nicht mehr stark umbauen oder komplett austauschen. Da jedoch bis 2030 alle Verpackungen recyclingfähig sein müssen, ist ein baldiges Handeln unabdingbar. Ich kann nur jedem raten, sich den gesamten Stoffstrom anzuschauen und sich ein Gesamturteil zu bilden.
Gesamturteil ist ein gutes Stichwort. Sie bemängeln, dass noch immer ein viel zu großes Silo-Denken stattfindet.
Das 17. UN-Nachhaltigkeitsziel fordert ‚Partnerschaften zur Erreichung der Ziele‘. Das kommt bislang noch viel zu kurz. Jeder betrachtet nur seinen eigenen Schreibtisch. Wir müssen lernen, von der Basis her zu denken. Wo kommen die Rohstoffe her? Bis wohin werden Produkte in ihrem zweiten Leben eingesetzt?
Kunststoff ist der Werkstoff des 21. Jahrhunderts, über alle Bereiche des Lebens hinweg – darin sind sich die Experten einig. Einen „funktionierenden“ Recycling-Kreislauf gibt es über die Dualen Systeme lediglich bei Verpackungen. Damit auch andere Kunststoff-Produkte im Kreislauf bleiben können, kann über alternative Verfahren nachgedacht werden. Hier kommt z.B. chemisches Recycling ins Spiel – hier mag der Einsatz Sinn machen. Aber um das nochmal klar zu sagen: Nicht bei Verpackungen, da haben wir mit dem mechanischen Verfahren eine viel ökonomischere und ökologischere Lösung.
Setzt die Politik denn die richtigen Leitplanken?
Eine Plastiktüte zu verbieten, ist sicherlich Aktionismus. Denn es gibt keinen Beleg dafür, dass die Plastiktüte besonders böse ist. Aber man muss auch manchmal Zeichen setzen. Ich führe das darauf zurück, dass wir als Industrie der Politik bisher zu wenige Angebote gemacht haben, um neue Wege aufzuzeigen.
Hier kommt die Mindestrezyklatquote ins Spiel. Wir stehen heute vor dem Problem, dass wir nicht genügend Rezyklate einsetzen. Jeder einzelne schaut aktuell, ob er nicht „vom nächsten Schreibtisch“ in der Wertschöpfungskette eine Lösung bekommt. Aber wir betrachten nicht die gesamte Prozesskette. Das ist der falsche Ansatz. Bei Maag setzen wir auf ein hochwertiges stoffliches Recycling. Da dies mit PP problemlos möglich ist, ist das chemische Recycling für uns keine Option. Ich würde mir wünschen, dass mehr Unternehmen auf PP setzen und das chemische Recycling nur in Ausnahmefällen ergänzend zum Einsatz kommt.
Unser Ziel muss aber Klimaneutralität sein. Wo ich die Rezyklate am Ende einsetze, ist völlig egal. Hauptsache, ich ersetze damit fossile Rohstoffe. Dass eine Verpackung wieder zu einer Verpackung werden muss, diese Diskussion gibt es nur bei uns. In der Papierindustrie wird aus einer Lebensmittelverpackung auch nie wieder eine Lebensmittelverpackung, sie wird immer Wellpappe oder Karton. In unserer Industrie machen wir ein Fass auf und reden über Open und Closed Loops und sagen, dass ‚echtes‘ Recycling nur dann stattfindet, wenn eine Verpackung wieder zu einer Verpackung wird.
Dieser Ansatz erklärt sich mir nur, weil es Vertreter gibt, die so ihr heutiges Geschäft sichern wollen. Es ist notwendig, dass sich Interessenvertreter zusammensetzen und erkennen, dass sie einen neuen Weg gehen müssen, um etwas zu verändern.
Sie haben bei Maag eine Menge verändert. Welche Entwicklung hat Sie in puncto Innovation besonders nach vorne gebracht?
Unsere Industrie ist sehr technologiegetrieben. Daher sprechen wir immer über das Produkt. Bei Maag sind wir jedoch anders vorgegangen. Wir haben uns die Organisation angeschaut und die Aufwände in jedem Bereich des Unternehmens reduziert. Das war die beste Innovation, denn wir sind jetzt viel effizienter aufgestellt. Diesen Prozess haben wir 2010 gestartet und uns von Bereichen, Produkten, Maschinen, Kunden und Märkten getrennt, in denen wir nicht gut waren.
Gleichzeitig haben wir uns Ziele gesteckt in den Bereichen, in denen wir richtig gut sind. So haben wir unsere Mitarbeiterzahl um 35 Prozent gesenkt, machen aber genauso viel Umsatz. Die Dinge, die wir jetzt tun, beherrschen wir viel besser. Deshalb ist jetzt auch unser Ziel wieder Wachstum – auch an Mitarbeitern.
Durch den Prozess haben wir uns viele Freiräume geschaffen. Unsere beste Innovation war, dass ich jetzt die Zeit habe, mich um strategische Dinge zu kümmern. Wir haben so viel Effizienz gewonnen, dass wir im deutlich zweistelligen Bereich Kosten eingespart haben. Tun es uns andere Firmen gleich, sparen sie ebenfalls. Machen das zwei Firmen gemeinsam, sparen sie noch mehr. So lässt sich beispielsweise auch der Materialeinsatz durch eine effizientere Lieferkette optimieren.
Es kommt letztendlich gar nicht darauf an, ob bei einer einzelnen Verpackung etwas mehr oder weniger eingesetzt wird. Die Lösung liegt in einem kombinierten Ansatz. Wir müssen Prozesse verbinden und digitalisieren – eine solche Symbiose sorgt für eine deutlich höhere Effizienz.
Arbeiten Sie deshalb auch eng mit NGOs zusammen?
Ja, ich habe es mir zur Aufgabe gemacht, nicht nur mit der Industrie zusammenzuarbeiten, sondern auch mit NGOs. Wenn wir Ideen haben, prüfen wir immer, wie sie dazu stehen. Bei den NGOs sitzen viele engagierte, fachkundige Menschen, die mir bestätigt haben, dass unser Ansatz der richtige ist.
Wir sind heute in der Lage, Ökologie und Ökonomie miteinander zu verbinden. Wir müssen nicht Klimaschutz auf Kosten von finanziellen Ergebnissen machen, Klimaschutz ist Teil des finanziellen Ergebnisses.
Stehen Sie mit Ihrem Unternehmen schon dort, wo sie hinwollen?
Wir sind seit diesem Jahr klimaneutral in unserem Tun. Mehr als 95 Prozent unserer Verpackung ist bereits kreislauffähig. Aktuell sind wir in Gesprächen mit vielen Marktteilnehmern, um die Dinge weiterzuentwickeln und die Ausschleusung des PP-Flexstroms weiter zu forcieren. Diesen Weg werden wir weiter beschreiten.
Vielen Dank Herr Schonlau für das Gespräch!
Über Ansgar Schonlau
Ansgar Schonlau ist Geschäftsführender Gesellschafter bei der Maag GmbH. Er ist ein internationaler Verpackungsexperte und besitzt mehr als 25 Jahre Erfahrung in der Druck- und flexiblen Verpackungsindustrie. Schonlau hatte verschiedene Vertriebs- sowie Managementfunktionen inne und stets das Ziel, die besten und kostengünstigsten Lösungen und Prozesse zu finden.
Über Maag GmbH
Die Maag GmbH wurde 1982 durch Jürgen Maag gegründet und Anfang 2018 von Ansgar Schonlau übernommen. Das international ausgerichtete, inhabergeführte Unternehmen bietet zuverlässige Lösungen für die Dienstleistung und Veredelung rund um flexible Verpackungen. Die Leistungen reichen vom hochwertigen HD Flexodruck über die Kaschierung aller gängigen Folienverbunde bis hin zur Laserperforation. Täglich beliefert Maag weltweit Unternehmen aus der Lebensmittelindustrie und aus der Hygiene- sowie Gesundheitsbranche mit hochwertigen Verpackungslösungen.