The race is on – the first coronavirus vaccines have been delivered and are being deployed. And additional batches follow each week. What is likely to be the largest vaccination campaign ever seen in history is set to launch around the world in the next few months. Despite the current political controversy about the low number of vaccine doses and the slow pace of vaccination – which it is hoped are just teething troubles – the project is also a mammoth logistical task.
At the forefront are also several German manufacturers of plastic packaging who, as refrigeration experts, are contributing to the success of the COVID vaccines with their refrigerated boxes.
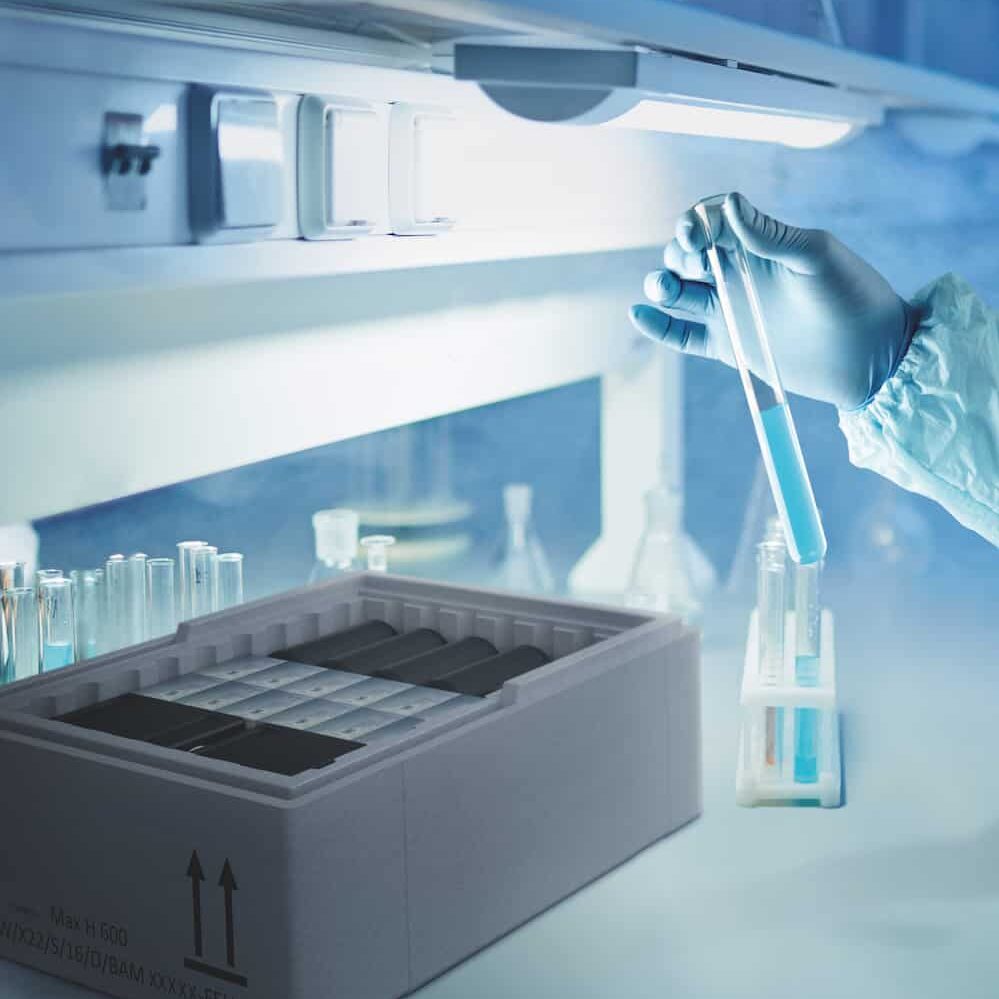
Reusable transport packaging made of EPS from the FEURER Group for pharmaceutical, chemical and laboratory transportation – for shipping without outer packaging and without cardboard containers.
After all, vaccines targeting COVID 19 are very complex products, each with very different requirements. This applies not only to production, but also to logistics. Efficacy, quality and safety as well as the rapid supply of sufficient vaccine to the population have top priority.
The fragile COVID 19 vaccines need to be transported safely to all parts of the world without interrupting the cold chain. This is because, in contrast to conventional vaccines – against influenza, for example – the new types of vaccines usually have to be stored and transported frozen at temperatures found at the South Pole.
15 million cool boxes
A study conducted by DHL and McKinsey highlights the challenges that transportation poses: Shipping ten billion units of vaccine worldwide involves transporting 15 million cold boxes on some 200,000 pallets on 15,000 cargo flights.
Add to this the further distribution within the countries all the way to the vaccination sites as well as the care and nursing homes for the elderly – the ‘last mile’. The federal government is responsible for the distribution of the vaccine within Germany, and each state is expected to have sufficiently dimensioned logistics.
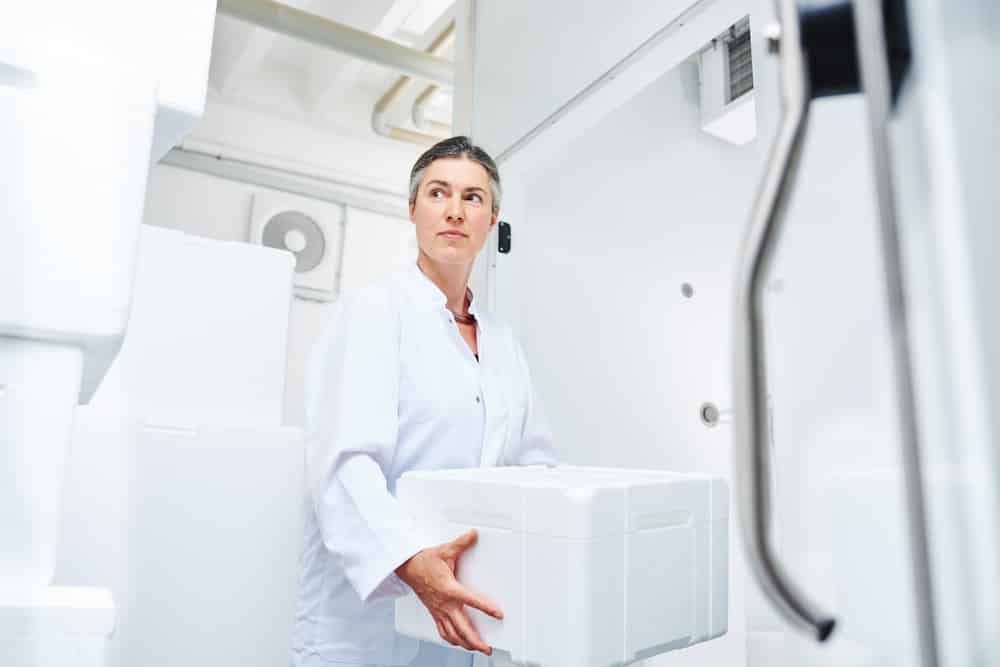
Plastic cool box from Storopack
Logistics specialists and pharmaceutical manufacturers have to choose the right transport solution because the required temperature ranges differ depending on the vaccine. Only boxes and packaging that have undergone the demanding testing and qualification processes and, for example, have maintained the required temperatures over an extended period of time are granted approval for this purpose.
Ultra deep freeze – ice cold is not cold enough
The artificial vaccine produced in the laboratory by BioNTech is based on innovative mRNA technology. There are as yet hardly any data on the chemical stability of such vaccines due to the very rapid development time.
The active ingredient from BioNTech is therefore transported at a particularly cold temperature of minus 70 degrees in order to avoid risks. “Ultra deep freeze” is the name given to such temperature requirements in logistics. The protective envelope of the mRNA in Moderna’s vaccine is slightly different from that of the BioNTech vaccine. It consists of lipid nanomolecules, which means that a temperature of just minus 20 degrees is sufficient.
The right transport box for every temperature
However, the different, sometimes extreme temperature requirements are no problem for the manufacturers of specially certified transport boxes. BioNTech, Pfizer, Moderna and co as well as their transport companies can choose from a range of special cool boxes.
Multiple demands on packaging
Storopack also offers a number of qualified solutions covering different temperature ranges. The packaging specialist can also guarantee transportation down to minus 70 degrees.
The boxes reliably maintain the temperature in the required cold range for a defined period while on the move and at the same time protect against damage. Cold packs or dry ice, for example, are used for cooling.
In addition, Storopack also offers packaging solutions down to minus 20 degrees as well as at 2 to 8 degrees. These are suitable, for example, for the transport of Moderna vaccines, which gained approval as a second vaccine in Europe. The vaccines from the US manufacturer only require a temperature of minus 20 degrees for transportation and storage.
Shipping time also plays an important role, of course. Depending on the requirements and the particular supply chain, Storopack’s insulated boxes can maintain the required temperature for up to 12, 48 or 72 hours. This also allows transportation through several countries within Europe where necessary.
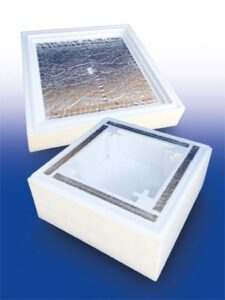
High performance O-Box H250 from OHLRO
Storopack boxes are available as disposable or reusable solutions and are made of expanded polypropylene (EPP) or expanded polystyrene (EPS*) – commonly known as Styrofoam.
Constant temperature for more than 10 days
The O-Box H250 cold box from OHLRO can maintain a constant temperature range of between 2 and 8 degrees over a period of 250 hours. The box has a patented cooling system and consists of a polystyrene box with combined cooling technology. Vacuum elements located in the hollow chambers of all outer walls provide optimum protection against heat exchange with the outside world.
A separate division within the Schaumaplast Group develops, qualifies and produces thermal packaging for the pharmaceutical industry under theThermoconbrand. Thermocon systems are used to transport a wide range of temperature-sensitive products, from coronavirus test kits, organs and cancer drugs to animal semen. When it became apparent in the summer that the BioNTech coronavirus vaccine would need to be stored and transported at -70°C, Schaumaplast engineers began qualifying thermal boxes of various sizes using dry ice as the cooling medium.
This led to solutions ranging from 1 litre product space to insulated containers that can hold an entire Euro pallet. A temperature of -70°C is reliably maintained for more than five days, even in summer outdoor temperatures. Thousands of vaccine doses have already been safely delivered to their destination at the right temperature in the Styrofoam and Neopor boxes. “It is a very special time for Schaumaplast. The whole team has worked hard and is now happy to see its products in use,” reports Managing Director Markus Hoffmann
As with all manufacturers of the cool boxes for the transportation of vaccines around the world, demands placed on the cooling system are high: Thermocon talks about a special foam, a special structure of the box and specially developed cooling liquids that release or buffer cold in doses.
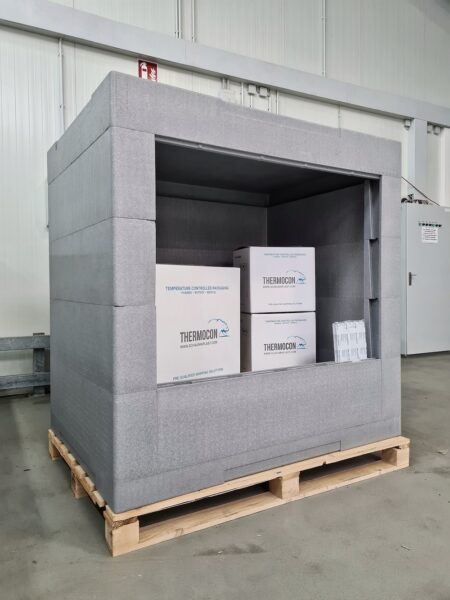
Pallet thermobox from Schaumaplast/Thermocon
“This is because the difficulty is to deliver the cooling energy that you put into the box in such a constant way that it is not too cool at the beginning of the transport and too warm at the end. We have to follow special procedures for this in order to be able to maintain a constant temperature in the box,” says Bernhard Hauck, Managing Director of the Schaumaplast Group.
The unusual grey appearance of the actual white EPS (airpop/expanded polystyrene) for the consumer results from the admixture of graphite, which further increases insulating performance. Originally developed by BASF for insulating buildings, the material now makes an important contribution in the vaccine cold chain.
Excellent Airpop packaging
FEURER‘s modular packaging for the pharmaceutical and chemical industries is also suitable for transporting vaccines. The packaging manufacturer developed the world’s first EPS hazardous goods packaging without outer carton, which was also recently awarded the WorldStar Award the packaging industry’s highest global award.
The airpop packaging, which consists of around 98 percent air and two percent plastic and is fully recyclable, is suitable for transporting refrigerated materials in parcels worldwide within 72 hours. The temperature range extends from plus 2 to plus 8 degrees to as low as minus 20 degrees.
Plastics packaging industry well prepared
Logistics will not be an obstacle to the rapid and safe supply of vaccines to the general population. Packaging companies are well prepared and play a system-relevant role in this process.
* What is EPS?
In 1949, BASF scientist Dr. Fritz Stastny invented what is known as “expanded polystyrene (EPS)”. EPS is extremely light. It consists of 98 percent air and two percent polystyrene and can be recycled several times.