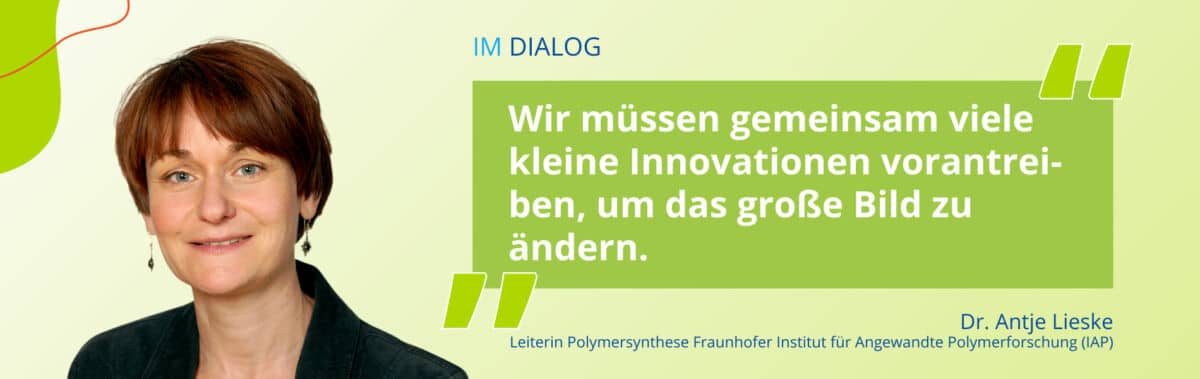
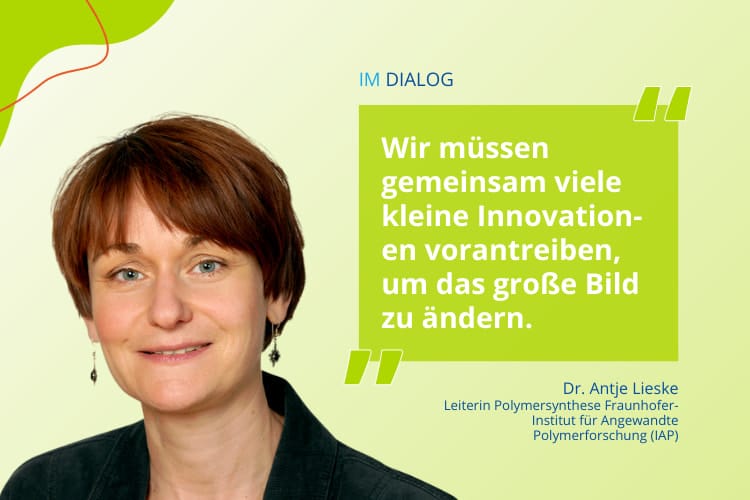
Dr. Antje Lieske, Leiterin der Abteilung Polymersynthese am Fraunhofer-Institut für Angewandte Polymerforschung in Potsdam (IAP), hat gemeinsam mit ihrem Team ein neuartiges Folienmaterial auf Basis des Biokunststoffes Polylactid (PLA) entwickelt. Wir haben mit ihr über die Besonderheiten des neuen Biokunststoffes gesprochen, warum diese Entwicklung überhaupt notwendig ist und welche Rolle Biokunststoffe in Zukunft einnehmen.
Frau Dr. Lieske, welche Rolle spielen Kunststoffe in einer nachhaltigen Kreislaufwirtschaft?
Kunststoffe sind dabei sehr wichtig, denn sie sind sehr leicht und trotzdem stark. Sie sind sehr widerstandfähig sowohl gegen mechanische Belastung als auch gegen chemische Einflüsse, zudem lassen sie sich sehr gut an unterschiedliche Anforderungsprofile anpassen.
Betrachtet man unsere Welt, stellt man fest, dass die meisten Menschen nicht ohne Kunststoffe leben wollen oder könnten, denn das wäre ein komplett anderes Leben als das aktuelle. Da muss man nur einmal einen Blick auf die Medizin werfen.
Wir müssen eine Kreislaufwirtschaft anstreben, denn anders wird diese Welt keinen Bestand haben. Ein so wichtiger Werkstoff wie Kunststoff muss integraler Bestandteil dieser Kreislaufwirtschaft sein. Deshalb ist es entscheidend, dass wir Konzepte entwickeln, wie dieser Kreislauf konkret gestaltet werden kann. Recycling spielt dabei eine zentrale Rolle, jedoch treten immer wieder Materialverluste auf, die ausgeglichen werden müssen. Um diese Verluste zu kompensieren, ist es notwendig, Biomasse als zusätzlichen Input in diesen Prozess einzubeziehen.
Was macht die Abteilung Polymersynthese am Fraunhofer IAP genau?
Als Materialentwicklerin beschäftige ich mich mit Polymersynthese, was verschiedene Aspekte umfassen kann. Z.B. kann es bedeuten, dass jemand aus Biomasse einen Baustein isoliert, der für den Einsatz in Polymeren geeignet ist. Unsere Aufgabe ist es dann, herauszufinden, wie sich aus diesem Baustein ein Polymer herstellen lässt – angefangen beim Reaktionsmechanismus bis hin bis zu den gewünschten Eigenschaften des fertigen Polymers. Der größte Teil unserer Arbeit konzentriert sich dabei auf Forschung und Entwicklung.
Darüber hinaus ist auch Kreativität gefordert. Wir schauen uns verschiedene Monomere, die aus nachhaltigen Quellen kommen, an und überlegen, welche Kunststoffe sich daraus entwickeln lassen. Das Monomer kann aber auch aus dem chemischen Recycling von Kunststoffen stammen. In diesem Fall bewerten wir die Qualität und geben Rückmeldung, ob es für die Polymerherstellung geeignet ist oder nicht.
Aktuell machen sich viele Branchen und Hersteller Gedanken um die Recyclingfähigkeit ihrer Kunststoffverpackungen. Worauf führen Sie das zurück?
Das liegt meiner Meinung nach an einer Reihe von Gesetzesinitiativen, die auf EU-Ebene im Verpackungsbereich beschlossen wurden und Unternehmen zwingen, zu recyceln.
In Bezug auf biobasierte Polymere gab es früher zwei große Treiber: Der erste ist Moral in Familienunternehmen, die sich auf die Fahne geschrieben haben, nachhaltig zu werden. Sie haben dieses Vorhaben in ihre Firmenstrategie verankert, obwohl dies mit hohen Kosten verbunden war. Oft scheiterte es jedoch daran, dass keine biobasierten Monomere aus lebensmittelrelevanten Rohstoffen verwendet werden sollten, sondern aus Biomasse der zweiten Generation, wie z.B. Stroh. Allerdings gab es keine Prozesse, die zufriedenstellend funktioniert haben. Es gab diesen Gedanken, etwas nachhaltig bewegen zu wollen, aber es sollte von Anfang an richtig gut sein.
Und was war der zweite Treiber?
Das war ganz klar der Werbeeffekt. Unternehmen, die durch ihre PR vermarkten lassen wollten, dass sie nachhaltiger sind. Das eine schließt das andere aber nicht aus. Auch für ein Unternehmen, das mit Überzeugung eine Nachhaltigkeitsstrategie vorantreibt, bringt das natürlich gute PR.
Was waren bisher limitierende Faktoren beim Einsatz neuer Ausgangsstoffe für Kunststoffe?
Die große Limitierung besteht einerseits im Preis, der je nach Einsatzbereich des Polymers immer noch eine Herausforderung darstellt, je nachdem wie hoch die Marge ist. Darüber hinaus spielt die Sicherheit der Rohstoffquellen eine wichtige Rolle. Es muss sichergestellt sein, dass Rohstoffe über mehrere Jahre hinweg in gleichbleibender Qualität verfügbar sind. Eine Herausforderung da Materialien, die in der Natur vorkommen, Schwankungen unterliegen. Ein weiterer Faktor sind die nicht optimalen Eigenschaftsprofile der Materialien. Damit beschäftigen wir uns am Fraunhofer IAP.
Ihrem Team ist es gelungen, ein neuartiges Folienmaterial auf Basis des Biokunststoffs Polylactid (PLA) zu entwickeln. Warum ist diese Entwicklung neuartiger Biokunststoffe überhaupt notwendig?
Möchte man die Biomasse effizient nutzen, kommt Polylactid (PLA) ins Spiel. PLA ist einer der am meisten eingesetzten Biokunststoffe und relativ preiswert. Die Idee ist, LDPE mit PLA nachzustellen. Reines PLA ist spröde und lässt sich überhaupt nicht ausdehnen, LDPE hingegen ist gar nicht spröde und sehr biegsam. Daher ist es notwendig, das Eigenschaftsprofil von PLA grundlegend zu verändern. Die Herausforderung besteht darin, diese Anpassungen je nach Anwendung vorzunehmen. Genau das ist Materialentwicklung: Auf Basis einer bestehenden Struktur möglichst wenig zu verändern, während man die gewünschten Eigenschaften maximal beeinflusst.
Wie sind Sie bei Ihrer Forschung vorgegangen?
Wir haben dieses Projekt von Anfang an mit dem Unternehmen SoBiCo GmbH zusammen umgesetzt, die Zielrichtung war klar definiert: flexible, nachhaltige Verpackungen. Zunächst haben wir den aktuellen Stand betrachtet und dann gegenübergestellt, wo wir hin wollen und welche Möglichkeiten dazu bereits existieren. Alles was es in der Literatur schon gab, haben wir ausgeschlossen.
Wir hatten die Idee, einen Weichmacher in die PLA-Kette einzubringen. Anschließend haben wir im Labor eine Proof of Principle durchgeführt: Lässt sich die Struktur überhaupt synthetisieren und bringt diese synthetisierte Struktur das gesuchte Eigenschaftsprofil mit? Anschließend vertieften wir uns in die Materialentwicklung.
Was bedeutet das?
Wir haben letztlich eine Matrix aufgestellt und überprüft, welche Eigenschaftsveränderungen bestimmte Strukturänderungen zur Folge haben. Daraus ergab sich ein Gesamtbild und wir wussten, wie man zu dem Material kommt. Die größte Herausforderung lag dann aber darin, dieses Material für die Verarbeitung zu optimieren.
Warum war das so schwierig?
Das neue Polymer muss von einem folienverarbeitenden Unternehmen verarbeitet werden können – und das mit den bestehenden Maschinen, ohne den Verarbeitungsprozess neu aufzusetzen. Die Verarbeitungseigenschaften so zu verändern, dass das funktioniert, hat sehr viel Zeit in Anspruch genommen.
Wie lange hat die Entwicklung insgesamt gedauert?
Eine solche Entwicklung braucht immer viel Zeit. Es hat acht Jahre gedauert, bis die Produktionsanlage für PLA-Folien eröffnet wurde. Für die grundlegende Materialentwicklung haben wir rund vier Jahre benötigt, die restlichen vier Jahren haben wir darauf verwendet, das Polymer verarbeitbar zu machen.
Das hört sich nach einem langen Zeitraum an. Man darf aber nicht vergessen, dass es beispielsweise Jahrzehnte gedauert hat, bis sich aus Polyethylenterephthalat, also PET, Flaschen produzieren ließen. Das sieht heute keiner mehr. Jetzt soll innerhalb von drei Jahren ein Material komplett neu entwickelt werden, das genauso performt wie das Bekannte. Das funktioniert nicht.
Was ist das Besondere an Ihrem neuartigen PLA?
Das neue PLA-Blockcopolymer ist zu mindestens 80 Prozent biobasiert und kommt mit seinen mechanischen Eigenschaften an LDPE heran. Darüber hinaus hat es sich zu einer Art Baukasten entwickelt. Wenn wir an bestimmten Strukturbestandteilen drehen, z. B. Menge, Länge oder Art des Weichblocks ändern, erhalten wir unterschiedliche Materialien. Hier geht es nicht mehr nur um Verpackung, es eignet sich zum Beispiel auch für den 3D-Druck oder Spritzgussbauteile.
Das Spannende ist, dass sich mit einer Grundsatzstruktur ein sehr breites Eigenschaftsportfolio abdecken lässt. Und alle diese Strukturen können auf einer Anlage produziert werden.
Um PLA zu recyceln, ist dann ein separater Strom notwendig?
Ja, daran arbeiten wir gerade. PLA lässt sich ziemlich gut recyceln. Es wird aus dem ringförmigen Monomer Lactid hergestellt. Diese PLA-Kette zerlegt sich, wenn man sie auf Temperaturen von 200 bis 250 Grad aufheizt, wieder in das Monomer. Das ist ein schöner Recyclingprozess. So ist nicht nur Downcycling möglich, sondern aus dem recycelten Monomer entsteht wieder Material in Neuwarequalität.
Wird das PLA-Material bereits kommerziell eingesetzt?
Die Anlage von SoBiCo wurde 2023 eröffnet. Jetzt befinden wir uns gerade in der Phase, einen Markt aufzubauen. D. h., es werden Muster für potenzielle Kunden hergestellt, um herauszufinden, wie Zustimmung ist und wo die Reise hingeht.
Sind Biokunststoffe in Zukunft ein Gamechanger?
Ein Material allein kann das selten haben, denn es ist auf bestimmte Anwendungszwecke ausgerichtet. Zudem wird PLA teurer sein als Polyethylen. Hinzu kommt, dass PLA aufgrund seiner Eigenschaften nicht für jede Anwendung geeignet ist: Es hat zum Beispiel keine so hohe Feuchtigkeitsbarriere wie Polyethylen. Dafür hat es andere Eigenschaften, die für bestimmte Einsatzzwecke prädestiniert sind.
Für unseren Partner SoBiCo ist diese Entwicklung dennoch lohnend. Um echte Gamechanger zu entwickeln, müssen wir an vielen Stellen gemeinsam arbeiten und kleine Innovationen vorantreiben, um das große Bild zu ändern. Es gibt nicht die eine Lösung, die uns retten wird, es sind ganz viele kleine Puzzleteile.
Was können Unternehmen tun, um die Forschung zu unterstützen?
In erster Linie müssen Unternehmen Geduld mitbringen und auf dem Schirm haben, dass solche Projekte Zeit benötigen. Zudem muss die Bereitschaft da sein, die notwendigen Investitionen zu tätigen. Darüber hinaus ist es hilfreich, wenn Unternehmen offen mit uns kommunizieren. Sie sollten die Bedarfe sowie die damit verbundenen Herausforderungen klar benennen, damit wir entsprechend darauf reagieren können.
Als Forschungsinstitut entwickeln wir vieles eigenständig. Einfacher wäre es, wenn mehr Unternehmen direkt auf uns zukämen und konkrete Probleme ansprechen würden, mit der Frage: Können wir das in einer Kooperation gemeinsam lösen?
Welche Unterstützung wünschen Sie sich von der Politik, um die Transformation hin zu einer funktionierenden Kreislaufwirtschaft voranzutreiben?
Es ist ein Dreiklang. Man muss Maßnahmen umsetzen, wie es jetzt mit der Verpackungsverordnung getan wird – also Restriktionen einführen. Darüber hinaus brauchen wir Anreize: Es müsste auch einen Bonus geben für diejenigen, die besonders gut recyceln.
Wenn ich mich mit nachhaltigen Polymeren beschäftige, ist die Verpackungsverordnung für mich widersprüchlich. Sie setzt im Wesentlichen auf Recycling – der Anteil aus recycelten Materialien ist festgelegt. Jetzt muss mir jemand erklären, wie biobasierte Polymere, die noch gar keinen Anteil am Recyclingstrom haben, in diesen Kreislauf gebracht werden können. Das ist aber notwendig, um Verluste auszugleichen.
Ich kann biobasierte Polymere nicht einfach durch Recyclinganteile verbessern, da es derzeit keine ausreichenden Mengen zum Recyceln gibt. Auch bis 2030 wird es noch nicht genügend Material geben, um es für Recyclinganlagen relevant zu machen. Unternehmen werden durch die Verpackungsverordnung dazu bewegt, sich mit diesen Fragen auseinanderzusetzen. Die aktuelle Perspektive ist jedoch oft zu sehr auf den Status Quo fokussiert und berücksichtigt nicht die zukünftigen Entwicklungen und Bedürfnisse.
Vielen Dank für das interessante Gespräch!
Über Dr. Antje Lieske:
Dr. Antje Lieske ist Abteilungsleiterin Polymersynthese am Fraunhofer IAP. Sie hat Synthesechemie an der Humboldt Universität in Berlin studiert und promovierte in Zusammenarbeit mit Fraunhofer, der TU Berlin und BASF zum Thema Polymere Tenside. Anschließend beschäftigte sich Dr. Lieske rund zehn Jahre mit Heterophasenpolymerisationen bei Fraunhofer, bis sie sich vor etwa 20 Jahren nach einer Umstrukturierung auf nachhaltige Polymere fokussierte.
Für die Entwicklung des neuartigen Folienmaterials auf Basis des Biokunststoffes Polylactid wurde Dr. Antje Lieske gemeinsam mit Dr. Benjamin Rodriguez und André Gomoll mit dem Joseph-von-Fraunhofer Preis 2024 ausgezeichnet.
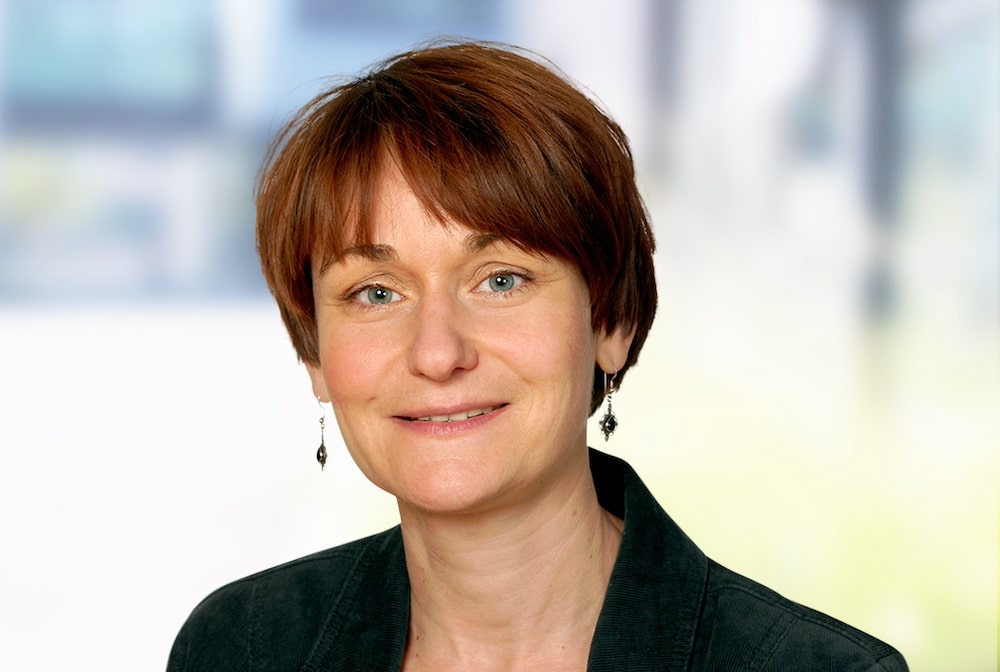
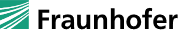
Über das Fraunhofer-Institut für Angewandte Polymerforschung IAP:
Das Fraunhofer-Institut für Angewandte Polymerforschung IAP in Potsdam ist zuverlässiger Partner der Industrie in den Bereichen Bioökonomie und Nachhaltigkeit, Energiewende und Mobilität, Gesundheit und Lebensqualität sowie Industrie und Technologie. Mit rund 260 Mitarbeitenden an sieben Standorten werden am Institut nachhaltige Materialien, maßgeschneiderte Prozesse und effiziente Technologien entlang der gesamten Wertschöpfungskette entwickelt – von der Idee bis zum industriereifen Prototyp.